matterlogoboss
Ansys Pressure Vessel Pdf
A few examples of performed by Pressure Equipment Engineering Services, Inc. Are as follows in PDF format:.Here are some more examples:. Fitness for service evaluations were performed for hundreds of vessels and experiencing generalized corrosion. Based on the half life criteria of the inspection codes, more frequent inspections must be performed for these vessels and heat exchangers to avoid violating the code or jeopardizing the safety of the equipment. In some cases, these vessels and exchangers start approaching scenarios indicating life depletion because of the loss of intended corrosion allowance.
The code calculations are performed (using Pressure Vessel calculations & Heat exchanger COMPRESS) for each component of the vessel / exchanger to calculate the minimum retirement thickness for that component for the intended design parameters. The combined set of minimum thickness for all components acts as a guide for future inspection interval for the vessel / exchanger. The calculated minimum thickness values are compared to the actual field measured values to make sure that there is sufficient future safe and useful life available for all the components of the vessel / exchanger. If enough life is not available for several components, then de-rating of vessel / exchanger may be necessary.
In case one or two components are limiting the MAWP, local repairs may be specified to maintain the original MAWP of the vessel / exchanger. Fitness for service evaluation was performed for several pressure vessels experiencing temperature lower than the MDMT.
The fitness for service criteria was used to evaluate the MSOT (Minimum Safe Operating Temperature) for the vessel. Based on the evaluation, it was concluded for some cases that the MSOT for the vessel was below the intended temperature of operation and thus the vessel was re-rated to the lower requested temperature.
However, when the MSOT for the vessel is above the intended temperature of operation, the vessel can not be re-rated to the lower requested temperature. Fitness for service evaluation for several tall vessels was performed before being subjected to in-situ PWHT at temperature of 1150 °F. Sometimes the vessel is heat treated for the circumferential zone containing the repair areas and at other times, the vessel is heat treated using gas firing such that the entire vessel is subjected to PWHT temperature. The actual vessel stresses due to dead weight and wind loading are calculated at the location of the circumferential PWHT zone and compared to the allowable stress values. For cases where the actual stresses are within the allowable stresses, the vessels can be post weld heat treated without any external support.
For the other cases, it is found that the vessel stresses exceed the allowable stress values. In these cases, it is recommended that the vessels must be supported with the help of a crane before PWHT is performed for the circumferential vessel zone. Fitness for service evaluation was performed for the top bed of a stainless steel reactor with the intent to calculate the maximum permissible pressure differential allowed by the structural capacity of the bed. The packed bed had 3 distinct stainless steel fabricated beams. The bed was getting plugged during operation.
Ansys Pressure Vessel Pdf Converter


This was causing significantly higher pressure drop on the bed leading to very high stresses in the beams. The intent was to shut down the reactor before the pressure drop reaches a scenario causing the structural failure of the bed. The structural calculations (per AISC code) were performed to check the stresses in the beams, welds and the beam support grating. These structural calculations were automated using MathCAD to calculate the maximum allowable pressure drop through the bed for design case, upset case and failure case. For each of these cases, the limiting pressure drop for the three distinct structural beams and the associated grating support was calculated. The design pressure drop through the reactor bed was 100 psig.
The maximum allowable pressure drop for the upset case was specified to be 138 psig. James bond mp3. At this pressure drop, all the design criteria were satisfied and this pressure drop was safely permissible.
The maximum allowable pressure drop for the failure case was specified to be 158 psig. At this pressure drop, the code allowable stress criteria were not satisfied and the structural components start to yield. Using the pressure drop guidelines specified by these set of calculations, the plant increased the safe operating time before the next shut down.
Fitness for service evaluation for a large spheroid vessel experiencing general corrosion. FEA using ANSYS was performed to complete the evaluation. The life of the vessel got extended by a few years. Some in the PDF format. Fitness for service evaluation for a horizontal reactor vessel for higher design loading.
FEA using ANSYS was performed to complete the evaluation. The results of the analysis indicated that we did not need additional stiffener rings as was being pointed out by conventional stress analysis.
Some in the PDF format. for the bottom head of a reactor experiencing pitting corrosion. FEA using ANSYS was performed to complete the evaluation. The life of the vessel got extended by a few years.
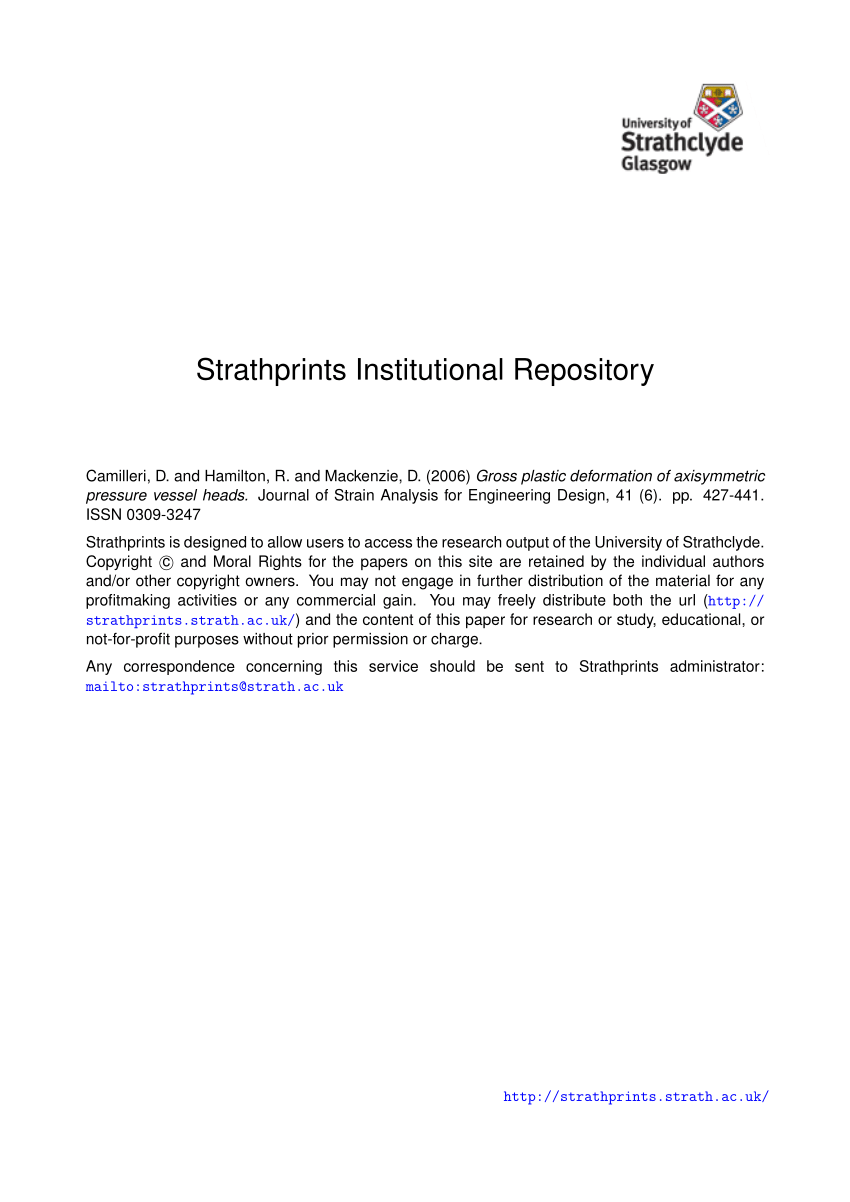
Some in the PDF format.